Search For Improvement With Complex Six Sigma
To understand what companies are doing to curtail costs while improving performance, <i>InformationWeek</i>'s sister publication, <i>Optimize</i> magazine, conducted a survey of 156 business-technology executives, asking them about their company's business-process frameworks, quality models, and technology standards
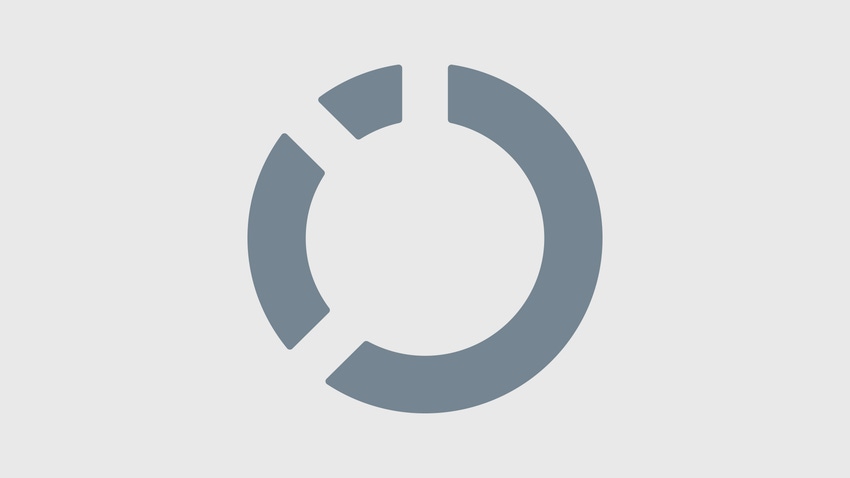
To understand what companies are doing to curtail costs while improving performance, InformationWeek's sister publication, Optimize magazine, conducted a survey of 156 business-technology executives, asking them about their company's business-process frameworks, quality models, and technology standards.
One process framework examined was Six Sigma. Using data and statistical analysis, this performance methodology works to improve profits and encourage greater efficiency by establishing defect-free processes and products. Defects can be chance factors--freak occurrences beyond one's control--or assignable factors where the source of a problem can be identified. To achieve complete Six Sigma compliance (that is, to attain Six Sigma Level 6), a process can't yield more than 3.4 defects for every million produced.
The fundamental objective of Six Sigma is the implementation of measurement-based strategies focused on reducing flaws, thus improving customer satisfaction.
Different tools and techniques can be used at different stages in implementing these measurement-based strategies. For example, the Design Customer Satisfaction and Manufacturing tool can be used for designing and manufacturing new products; another tool is Cross-Functional Process Mapping, for processes that run though an enterprise.
Achieving Six Sigma requires mastering several stages: defining the process in question, measuring its performance, analyzing its effectiveness, implementing improvements, and controlling improvements over the long term.
Mastering these steps helps companies attain Six Sigma, but this isn't an easy task. In fact, of the 156 business-technology executives surveyed by Optimize Research, fewer than 40% report their company even employs Six Sigma.
Share with us at the address below which process frameworks and quality models your company has found useful in achieving procedural improvement and consistency.
Helen D'Antoni
Senior Editor, Research
[email protected]
Tech Support
How has your company's IT department participated in establishing Six Sigma?
IT managers at companies using Six Sigma are finding themselves involved in its use. Nearly three in five business-technology executives surveyed report they keep tabs on Six Sigma third-party services providers. Nearly half say they're involved in training or change management, while slightly less have a say in Six Sigma strategies and policy making.
Outside Help
Did your company hire strategy consultants to help implement Six Sigma?
To ensure Six Sigma initiatives are most effective, companies aren't relying totally on in-house expertise to get the job done. Half of sites Optimize Research surveyed partner with a third-party consultant.
The most frequent arrangement has the consultant mapping out the use of Six Sigma in addition to assisting in its implementation. Nearly a third of sites using the business-process framework and working with a strategy consultant have this arrangement.
Deployment Hurdles
What challenges has your company faced in implementing Six Sigma?
Companies interested in using Six Sigma should include a corporate communications campaign as a key element in its rollout. When asked about the challenges they've encountered, respondents say the issues aren't related to money. Instead, resistance to change or lack of buy-in top the list of problems. Resistance was about the same at almost every level of the enterprise, including among employees, middle management, and senior executives. A lack of proper training among managers and executives exacerbates the problem.
Reported Payoffs
Have you been rewarded for attaining a level of expertise in Six Sigma?
For some, establishing a certain level of expertise in Six Sigma has had it payoffs. Of the 43 business-technology executives Optimize Research surveyed at sites using Six Sigma, more than half report that they've been rewarded for attaining some level of proficiency in Six Sigma. Nearly 30% say they were given a title change, slightly less than a quarter received a bonus, while one in five got a pay increase. Another 12% report other accolades.
About the Author(s)
You May Also Like
How to Amplify DevOps with DevSecOps
May 22, 2024Generative AI: Use Cases and Risks in 2024
May 29, 2024Smart Service Management
June 4, 2024