Intel Laser Chip Could Transform Future Data Centers
The chipmaker says it can create transceivers that operate about 1,000 times faster than the 1 Gbps to 10 Gbps connections currently used in data centers.
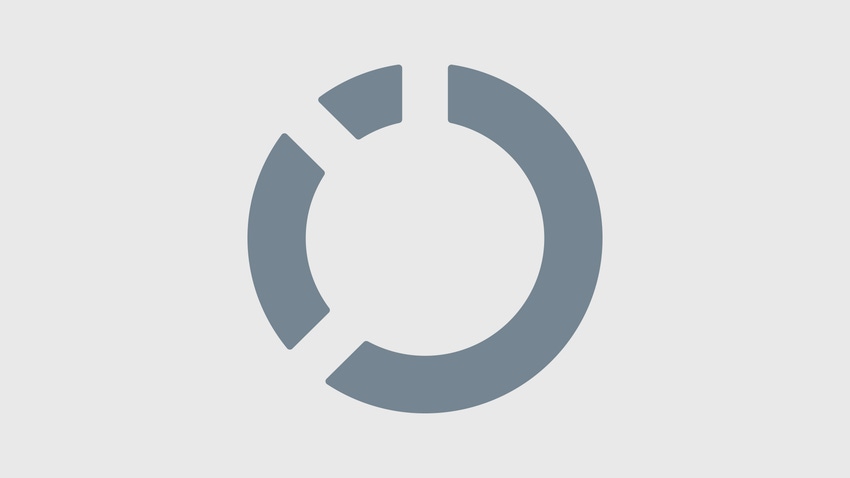
Intel's hybrid silicon laser, which the company says recently cleared a significant technology hurdle, could have tremendous impact on data centers, letting IT executives and data center managers rethink the layout of equipment and deployment of services.
Intel has demonstrated the ability to create lasers by combining Indium Phosphide material with standard and low-cost silicon using a traditional manufacturing process to create transceivers that can operate at 1 terabit-per-second speeds, or about 1,000 times faster than the Ethernet connections currently used in data centers that run at 1 Gbps to 10 Gbps speeds.
"Imagine that distances no longer matter," says Victor Krutul, director of silicon photonics strategy for Intel. "We can rearchitect the platform and start looking at new opportunities."
Traditional hardwired silicon transceivers provide the interconnection capabilities in most computers systems today, but are limited in range by the electrical properties of the metal wires used within the chips. The electrical signals on the wires create "noise" that limits the distance possible between the various components in a system, and distances between integrated computing platforms.
Optical devices do not generate noise, and are used in the telecommunications industry to transmit data over distances of 25 miles and greater. Researchers have long understood the potential benefits of optical interconnections, but the costs could run as much as $100,000 per connection, as compared to the $1 per connection that Intel is targeting for its hybrid silicon laser.
In addition to connecting various components like processors and memory within a PC or server, the optic-based technology can be used to connect boards to other boards and systems to systems.
"Imagine a little chip in a server sending data at a minimum of 1,000 times faster than today," Krutul says. "Imagine loading movies in seconds, practically in real time."
Inside the data center, designers using the optical interconnection capability in the future will no longer be limited to distances of 17 inches to 20 inches between interconnections. They will be able to spread-out high-density loads into more isolated areas, or create component "supercells" where large blocks of memory or microprocessors can be stored and shared across the enterprise, with their high heat loads isolated and dealt with by direct cooling technologies.
The silicon lasers will probably need around five years of more work before they can offered commercially, Krutul says. "We know how to build it," he says. "We've proven the science. We have all the individual components, and now we have to integrate them and make them fly."
The research is being done by Intel in cooperation with the University of California, Santa Barbara, where John Bowers, a professor of electrical and computer engineer, is a known expert in Indium Phosphide research.
The Indium Phosphide-based material is used for light generation and amplification while the silicon is used to contain and control the laser. The manufacture of the transceivers involves the use of a low-temperature electrically charged oxygen gas, to create a thin oxide layer on the surfaces of both materials.
When heated and pressed together, the oxide layer functions as "glass glue" to fuse the two materials into a single chip. When voltage is applied, light generated in the Indium Phosphide material passes through the oxide layer and into the chips waveguide, where it is contained and controlled, creating the hybrid silicon laser.
About the Author(s)
You May Also Like
How to Amplify DevOps with DevSecOps
May 22, 2024Generative AI: Use Cases and Risks in 2024
May 29, 2024Smart Service Management
June 4, 2024