The Heart Of Intelligent Manufacturing
The manufacturing execution system (MES) commands potentially valuable sources of information for strategic business applications that feed on intelligence.
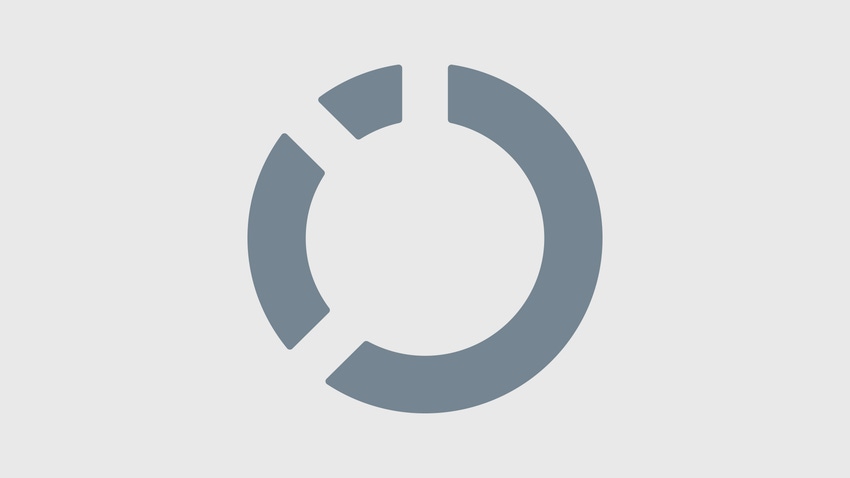
As stated earlier, MESs can come in all shapes and sizes and have one or more of the components outlined here, depending on the industry and user company. Some companies have all of these systems and more, but don't use the term "MES." In other instances, a company might call a single module — such as an SPC package — an MES system. Others will have an assortment of packages collectively referred to as an MES, but have no tie between the packages. MES doesn't have a broadly accepted meaning, especially among batch and process industries. It's also important to note that while core functions will generally be well integrated, most of the support functions won't. Newer applications pay more attention to data integration issues, but most execution systems are made up of disparate components.
Leveraging MES Information
Although in widespread use since 1985, business objectives for efficiency and efficacy in the supply chain are driving a surge of new interest in their MES applications and usefulness. A major reason is that these systems (both manual and computerized) and their components generate and maintain a large amount of data that could be useful to many more people within the enterprise as well as external value-chain partners on both the demand and the supply side. Historically, this information has been difficult to retrieve and include in more extensive user communities — that is, those beyond the plant floor. The good news is that information availability is improving as vendors recognize the need to enhance their applications with broader functionality, Web access, and newer tools that can collect and aggregate data from disparate systems.
In an upcoming article, I will focus more closely on how organizations will use MES data and information more broadly for IT systems. Briefly, here are some leading-edge ideas some organizations are using to broaden the use of this information:
Portals can aggregate and process manufacturing data for specific user communities. Portals can be used to share scheduling information across collaborative value chains.
Manufacturing intelligence systems can collect specific data from plant-focused devices and systems. Such systems can present information in dashboards and other KPI tracking systems.
Progress in business process management tools and application standards, such as RosettaNet, will improve linkage among global MES functions and support organizations building composite applications to serve the plants of a company and/or companies within a value chain.
Execution system providers are broadening their application footprints by offering greater functionality in their existing systems, or by providing additional, linked application packages. Rockwell Automation, GE, and Siemens are good examples of companies that have acquired an array of companies and products, enabling them to build integrated, single-source solutions for their business partners. Additionally, traditional MES technology providers, including Camstar, Datasweep, and Visiprise are extending their systems to include improved support for a wider variety of functions, including quality assurance, genealogy, product life-cycle management, and supply chain collaboration.
MESs have been in place for many years, with a primary focus of supporting first-line supervision. As the systems' use broadens to support a wider audience — a trend implied by intelligent enterprise and value chain collaboration concepts — the MES role will change. One key role is clear: The MES will have a growing impact as a critical source of real-time event information.
Michael McClellan is president of Collaboration Synergies, an advisory company focused on collaborative manufacturing systems development and implementation, plant floor information systems, and MES. He has more than 30 years of experience serving and managing manufacturing enterprises, and was a founder of Integrated Production Systems. He's the author of several books, most recently Collaborative Manufacturing: Using Real-Time Information to Support the Supply Chain (CRC Press, 2002).
Major Manufacturing Systems |
---|
Planning SystemsMaterial Requirements Planning (MRP), Manufacturing Resource Planning (MRPII), Enterprise Resource Planning (ERP)Planning systems have traditionally operated in batch and run on a planned basis. Thus, vendors' early versions of MRP, MRPII, and ERP systems similarly required operating cycles of one week or more. ERP vendors now employ architectures that can support online response times. Execution-Level Plant Floor SystemsMES, Warehouse Management Systems, Quality Assurance SystemsMost plant floor management systems are OLTP, operating in minutes or less. In most cases, the transaction frequency is less than that of typical computer systems applications. Device and Process Control SystemsProgrammable Logic Controllers (PLC), Systems Control and Data Acquisition Systems (SCADA), Process Control Computer SystemsSystems in this category operate in milliseconds, controlling processes and machine movements in real time. |
Resources |
---|
For more information about MESs, see www.mesa.org. The Manufacturing Enterprise Systems Association (MESA) is a vendor/user association that is focused on manufacturing systems applications. |
About the Author(s)
You May Also Like
How to Amplify DevOps with DevSecOps
May 22, 2024Generative AI: Use Cases and Risks in 2024
May 29, 2024Smart Service Management
June 4, 2024